Для полов по стяжке используем линолеумы на тепло- звукоизолирующей основе либо безосновные линолеумы укладываем на подложке из ДВП. Для полов по основе «дощатый или листовой "черный" пол» можно использовать любой линолеум как безосновный, так и на основе. Если дощатый пол имеет щели, то он должен быть зашпаклеван паркетной шпаклевкой либо по нему делается подложка из ДВП-Т, ДСП, ОБВ или фанеры. Иначе линолеум обожмет дощатый пол и «покажет» доски.
Современные бытовые линолеумы позволяют при настилке не мудрить со швами и подгонкой рисунка, а настилать полотнище одним куском на всю комнату, если ширина ее не превышает 4 — 5 м. Считается, что настилка линолеума одним куском более сложная, чем настилка его кусками. Однако это не так, уложить линолеум одним куском значительно проще и быстрее, чем заниматься прирезанием швов и подгонкой рисунка. Если размеры вашей комнаты позволяют настелить линолеум одним куском и вас устраивает его расцветка, то предпочтение нужно отдать именно ему, так как уложить его может человек никогда прежде этим не занимавшийся. Правда, одно осложнение при приобретении широких полотнищ линолеума все же есть: его трудно перевозить и заносить в подъезды «хрущевок». Хотя, если линолеум не ломкий, то это вполне возможно.
Для определения размера приобретаемого линолеума измерьте комнату, учтя ниши, альковы и эркеры. Сделайте при замере припуск на обрезку вдоль кривых стен 10 — 15 см по ширине (длине) комнаты и добавьте половину глубины дверного порога. Если требуется использовать несколько полотнищ, учтите припуски на совмещение рисунка. После приобретения линолеума занесите его в комнату, где он будет настелен и положите, не раскатывая, на сутки. Пусть полежит, акклиматизируется и примет температуру воздуха в помещении.
Линолеум укладывают на основание четырьмя способами: на клею, под всем полотнищем или только по периметру; на двухстороннем липком скотче, по периметру полотна и под стыками; с прикреплением к деревянной основе гвоздями и скобами; и «насухо», вообще без какого-либо крепления.
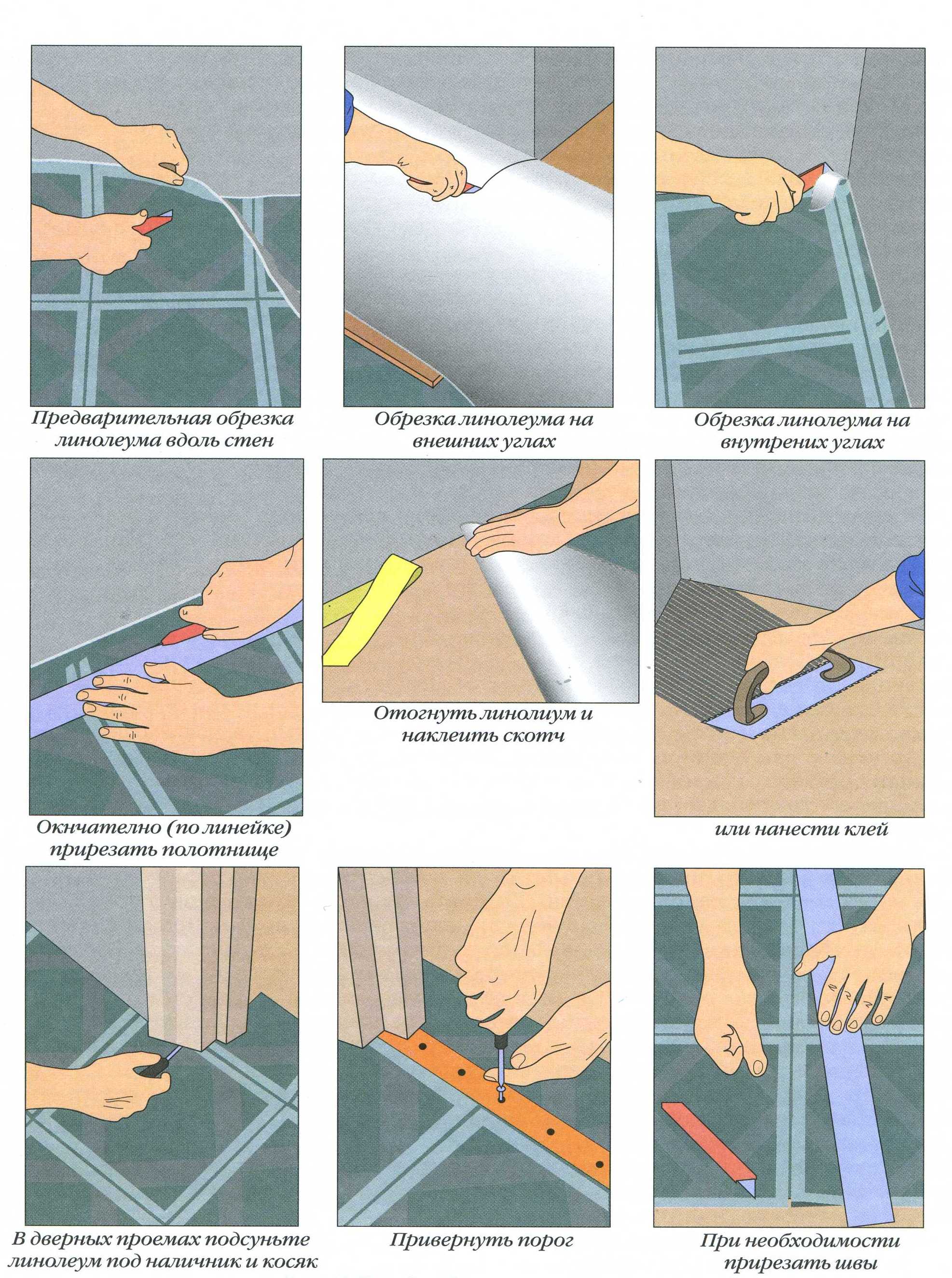
При использовании клеев применяйте
клеи, рекомендованные производителем линолеума, иначе клей вместо того, чтобы приклеить покрытие, может его растворить либо, наоборот, «намертво» приклеить материал к основе, так, что снять его потом будет проблематично. Одной из особенностей современных клеев для линолеумов является то, что они крепко держат покрытие в процессе эксплуатации, но когда требуется его сменить, линолеум легко отдирается, не оставляя на основании никаких следов. Для линолеума на теплоизолирующей подоснове применяют дисперсионные клеи (Бустилат, Гумилакс, АК, АДМ-К). Для линолеума на тканевой подоснове — битумные мастики — «Биски» и битумно-синтетический клей, а также дисперсионные клеи. Для линолеума без подосновы применяют мастики на основе синтетических смол и каучуков.
Обычно приклеивание линолеума к основанию производят в помещениях с высокой интенсивностью эксплуатации. Для домашних помещений вполне достаточно посадить линолеум на двухстороннюю липкую ленту (скотч) или уложить его насухо с проклейкой стыковочных швов, если таковые имеются.
Последовательность работ.
Расстилание и подъезда линолеума.
Плинтусы должны быть сняты. На подготовленном полу разверните рулон. Проверьте, правильно ли расположен рисунок. Разгладьте покрытие щеткой в направлении от центра к краям комнаты для удаления воздушных пузырей. Если размеры полотна значительно превышают размеры комнаты, то ножом или ножницами обрежьте покрытие из ПВХ приблизительно по размеру комнаты, оставив с каждой стороны по 5 см для окончательной подгонки. Если размер полотнища почти совпадает с размером комнаты, уложите линолеум с небольшими нахлестами на стены.
Металлической линейкой крепко придавите покрытие в угол между полом и стеной. Держа острый поделочный нож под углом 45 к линейке, обрежьте лишнюю часть. В конечном итоге линолеум нужно подрезать так, чтобы его края не доходили до стен примерно по 5 — 10 мм. Опасаться неровных надрезов не нужно, они прикроются плинтусом. Если настил линолеума ведется по деревянным полам, то подрезать его нужно таким образом, чтобы края линолеума свисали над щелью между деревянным полом и стеной. Пока неизвестно, как поведет себя линолеум после вылежки — сожмется он или расправится.
Свисающие над щелью концы можно потом подрезать, а если в результате сжатия полотнище окажется коротковатым, то придется прикрывать его уширенным плинтусом. У внешнего угла отогните полотнище назад, сложив (в два слоя) тыльной стороной вверх. Между слоями уложите древесноволокнистую плиту, чтобы не прорезать нижний слой. Ножом сделайте разрез до конца листа, начав в 5 см от угла, слегка отклоняя линию разреза в сторону «лишней» части. Во внутреннем углу сложите полотнище листа в форме буквы У и сделайте по центру разрез. Наложите два клапана внахлест и обрежьте по углу. Удалите обрезки и подогните концы на место. После прирезки линолеума оставьте его полежать на двое суток, пусть расправится.
Приклеивание полотнища.
Для нанесения клея отогните назад половину полотнища. Распределите клей по основанию зубчатой гладилкой. Дисперсионные клеи и мастики наносят зубчатым шпателем слоем 0,6 — 0,7 мм, на основе битумов — слоем 0,4 — 0,5 мм, на основе синтетических смол и каучуков — 0,3 — 0,4 мм. На дисперсионные клеи и мастики линолеум укладывают сразу после их нанесения на основание, а на клеи и мастики на основе битумов — через 15 — 20 минут. Клеи и мастики на основе синтетических смол и каучуков выдерживают для улетучивания избытка растворителя до «отлипа». После этого на тыльную сторону безосновного линолеума шпателем или кистью наносят клей слоем 0,2 — 0,3 мм. Через 10 — 15 минут после нанесения клея на тыльную сторону линолеум наклеивают на подготовленное основание. Если настилка линолеума производится несколькими кусками, то клей наносят под полотнище, оставляя сухим 10 — 15 см у кромки, которая будет стыковаться с другим полотнищем. Двухсторонний скотч при этом виде настилки, наклеивается только на основания без приклеивания его к линолеуму. Если линолеум настилается одним куском на всю комнату, то клей можно наносить на основание в виде сетки. Если вместо клея используется двухсторонний скотч, то его приклеивают к полу (по периметру помещения или в виде сетки с ячейками 50х50 см), не снимая верхней защитной пленки. Поверхность пола под скотчем должна быть обезжиренной, сухой и чистой. Затем снимают со скотча верхнюю защитную пленку и приклеивают покрытие.
Уложите полотнище и разгладьте. Уложите полотнище на второй половине комнаты. У дверного проема пропустите полотнище под наличник и под стойку дверной коробки, для этого наличник и коробку придется подпилить. Обрежьте край полотнища так, чтобы он проходил по центру дверного проема.
Стыковка двух полотнищ
При использовании двух полотнищ покрытия из ПВХ укладывайте их с одной и другой стороны комнаты таким образом, чтобы в месте стыка с обеих сторон были заводские кромки. При клеевой технологии крепления укладывайте кромки полотнищ с нахлестом 2 — 3 см и совмещением рисунка. При креплении на липкую ленту уложите полотнища «стык в стык>. Через двое суток линолеум даст усадку и стыкование можно доделать.
При укладке насухо или на скотч полотнища линолеума через двое суток просто пододвигают друг к другу с совмещением рисунка. Затем края шва отгибают и проклеивают основание, а потом и сам линолеум двухсторонним скотчем. По периметру помещения скотч, приклеенный к основанию, освобождается от верхней защитной пленки и на него «сажается» линолеум либо линолеум остается без приклейки — укладывается «насухо».
При клеевом креплении полотнищ сделайте разрез сквозь два слоя так, чтобы листы точно совпадали. Отогните края линолеума, промажьте основание клеем. Прижмите края к основанию, например, положите обрезок ровной доски и походите по нему.
Установка плинтусов и порога.
В заранее просверленные в стенах отверстия вставьте дюбели и саморезами прикрепите к стене плинтусы. Если основание пола было деревянным, то необходимо оставить щель для вентиляции подпольного пространства. Это делается просто. Перед прикреплением плинтуса между ним и покрытием пола вставляются полоски (обрезки) линолеума, таким образом получается щель между полом и плинтусом. После установки плинтуса обрезки линолеума вынимаются. Щель можно оставить и между стеной и плинтусом — это не принципиально. Между полом и плинтусом щель менее заметна, чем между плинтусом и стеной, однако в ней будет накапливаться грязь. Решать вам, рисковать полом и выбрать «эстетику», пренебрегая вентиляцией, либо делать вентиляционную щель. Правда, сегодня существуют системы с принудительной вентиляцией пола, но это недешево. Наконец, закрепите в дверном проеме пороговую планку. Подберите планку, подходящую к стилю покрытия в соседней комнате. Прикрепите пороговую планку к полу. В бетонном полу сначала сверлом для кирпичной кладки просверлите отверстия и вставьте в них пластиковые дюбели для шурупов.
На основе материалов книги Савельева А.А. "Полы в вашем доме"